Real-Time Standard
MeasurLink Real-Time Standard Edition is designed for customers who want to acquire and analyze data in real-time and check variable and attribute inspection to maximize production and minimize defects. It has views to allow the user to create Parts, Characteristics with nominal and tolerance and Traceability lists.
Learn More arrow_downwardRequest DemoProduct SupportDownload Brochure
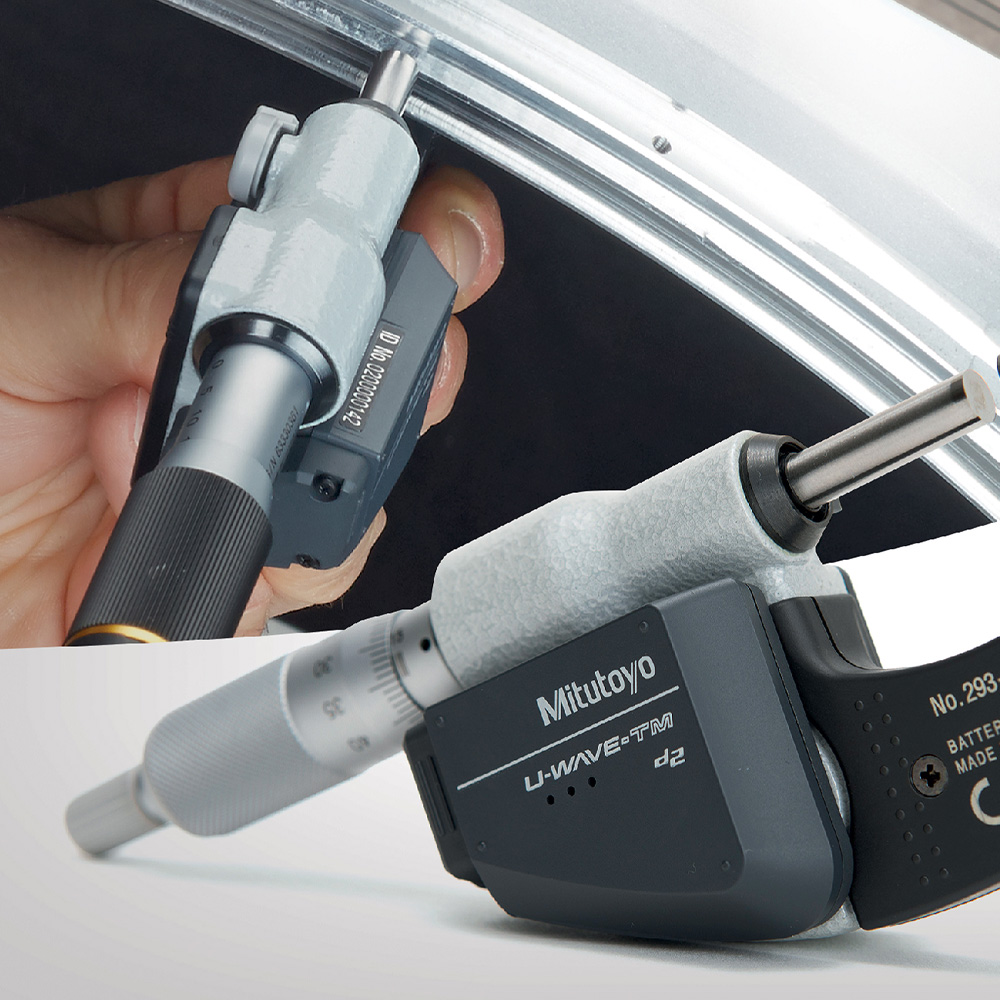
Designed to collect data at the point of manufacture, operators can be alerted of trends, cycles, and nonconformance as soon as they occur. A customizable user interface allows the user nearly infinite ways to view information specific to that process. MeasurLink Real-Time has the ability to connect and acquire data from virtually any measuring device. It supports the full range of metrology technology, including calipers, micrometers, indicators, CMMs, vision systems and more.
Features & Benefits
Click each feature to learn more.
Click a gage button and watch the charts update in real-time. This helps the operator stay on top of the process. Begin collecting data in minutes with the newly designed Inspection Wizard.
View scanned blueprints, digital photographs at a glance. On-screen guided sequencing keeps the operator moving to the right feature.
Easy to use Control Charts, Histograms, Capability, Detailed statistics, Assignable Causes, Corrective Actions, and Traceability all make this software “best in class”.
Allows characteristics of the same routine to be measured at different intervals while maintaining appropriate prompted guided sequencing.
Attach movies (AVI, MOV, MPG), sound (WAV) and images (BMP, JPG, TIF) to parts, routines or individual characteristics as instructional aides for an operator.
Track specification adjustments and preserve historical data.
Collects data from digital micrometers, calipers, indicators, bore gages, etc. Keyboard entry is a snap. Collect data for one or a million parts. Begin collecting data in 60 seconds with a “Quick Run” by defining features, tolerances and input method. Flexible data input. Collect data by feature, by part or randomly. Guided sequencing minimizes inspection errors.
Collect dimensional data (length, width, height, outside diameter, inside diameter weight, etc.). Supports derived features (calculations for run out, volume, true position, etc.). Mix your dimensions and non-conformance in the same Inspection Routine. Track defects and defectives along with your dimensional data. Collect data from visual inspections (burrs, cracks, dents, missing holes, etc.) to determine the fitness of a part. Track failures using a go/no-go style or count the defects on a characteristic to determine if a part is defective. There is complete flexibility to study the individual characteristics and as a group of them, too.
Create your own customized Crystal Reports for use with Part or Run data. Build report templates with company logos and free form text. Select and position chart types to customer specification.
Attach drawings to parts, routines or individual characteristics for viewing. Most file formats are supported as an attachment (e.g. Word, PDF).
Full support of Western Electric and Nelson Tests for pattern recognition in control charts (e.g. extreme point, trend, stratification, oscillation, etc.) along with various alerts for each failed test.
All observation data is marked with the date and time from the computer clock.
Operators choose corrective action as applied to the part or process. Multiple corrective actions can be applied to any subgroup. Empower operator to build on existing Corrective Action list.
Force Assignable Cause Tags on Inspector during collection if process is out of control. Empower operator to build on existing pick list.