Real-Time Professional
MeasurLink Real-Time Professional Edition enables customers to connect and acquire data from Mitutoyo Coordinate Measuring Machines, Vision and Form Measuring Systems via native integration (DDE).
Learn More arrow_downwardRequest DemoProduct SupportDownload Brochure
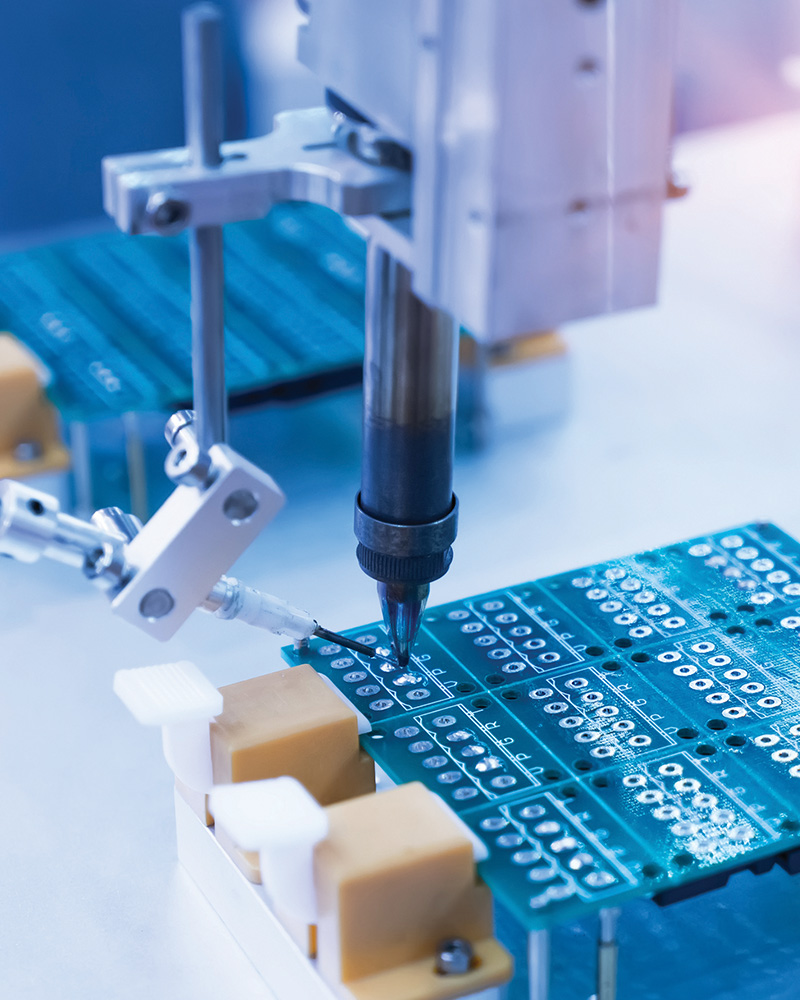
In addition to all of the features supported by MeasurLink Real-Time Standard Edition, this application also supports data filters. Full reporting functionality with templates is also provided. Supported data sources include keyboard, RS232 and USB devices, native Mitutoyo integration (DDE) ASCII and QMD (xml-based) file import. MeasurLink also supports the Quality Information Framework (QIF) through the import of QIF Plans and the export of QIF Results and Statistics.
Features & Benefits
Click each feature to learn more.
Easily create an import template that maps data in a text file to MeasurLink information. Templates are saved to the database for everyone to use and can be added as data sources to data collection stations. An import template can be verified against the source file without adding data to the system.
When set up as a data source, import templates are readily available to the operator, or periodic imports can be executed.
Collect data into MeasurLink from Mitutoyo capital equipment running Mitutoyo Software that is MeasurLink enabled. This provides a tighter and more robust interface than importing data from files.
All data collected within a Real-Time run is related. Often, especially for runs containing a large volume of subgroups, requests are made for subsets of data that are further related from the entire run’s population. MeasurLink provides robust filtering capabilities to comply with these requests.
Click a gage button and watch the charts update in real-time. This helps the operator stay on top of the process. Begin collecting data in minutes with the newly designed Inspection Wizard.
View scanned blueprints, digital photographs at a glance. On-screen guided sequencing keeps the operator moving to the right feature.
Easy to use Control Charts, Histograms, Capability, Detailed statistics, Assignable Causes, Corrective Actions, and Traceability all make this software “best in class”.
Allows characteristics of the same routine to be measured at different intervals while maintaining appropriate prompted guided sequencing.
Attach movies (AVI, MOV, MPG), sound (WAV) and images (BMP, JPG, TIF) to parts, routines or individual characteristics as instructional aides for an operator.
Track specification adjustments and preserve historical data.
Collects data from digital micrometers, calipers, indicators, bore gages, etc. Keyboard entry is a snap. Collect data for one or a million parts. Begin collecting data in 60 seconds with a “Quick Run” by defining features, tolerances and input method. Flexible data input. Collect data by feature, by part or randomly. Guided sequencing minimizes inspection errors.
Collect dimensional data (length, width, height, outside diameter, inside diameter weight, etc.). Supports derived features (calculations for run out, volume, true position, etc.). Mix your dimensions and non-conformance in the same Inspection Routine. Track defects and defectives along with your dimensional data. Collect data from visual inspections (burrs, cracks, dents, missing holes, etc.) to determine the fitness of a part. Track failures using a go/no-go style or count the defects on a characteristic to determine if a part is defective. There is complete flexibility to study the individual characteristics and as a group of them, too.
Create your own customized Crystal Reports for use with Part or Run data. Build report templates with company logos and free form text. Select and position chart types to customer specification.
Attach drawings to parts, routines or individual characteristics for viewing. Most file formats are supported as an attachment (e.g. Word, PDF).
Full support of Western Electric and Nelson Tests for pattern recognition in control charts (e.g. extreme point, trend, stratification, oscillation, etc.) along with various alerts for each failed test.
All observation data is marked with the date and time from the computer clock.
Operators choose corrective action as applied to the part or process. Multiple corrective actions can be applied to any subgroup. Empower operator to build on existing Corrective Action list.
Force Assignable Cause Tags on Inspector during collection if process is out of control. Empower operator to build on existing pick list.